This week, the trawler will embark on its maiden voyage. The delivery of the vessel concludes a two-year design and building process. The contract with VARD was finalised in April 2022 and is valued at over EUR 50 million.
More fuel efficiency
The main engine, by Bergen Engines AS, delivers 5400 kW, paired with a 2500 kW shaft generator. Caterpillar's auxiliary engine offers 1785 kW. The main engine optimises fuel usage through adjustable RPM (revolutions per minute) and VVT (variable valve timing), enhancing fuel efficiency across various loads. This approach builds on existing concepts, showcasing DFFU’s ongoing commitment to improving fuel efficiency and contributing to the industry's broader environmental responsibility and sustainable practices.
Extensive production capabilities
The vessel is equipped with the latest technology on an advanced processing deck built by Optimar. It was designed with the aim of utilising all the raw materials caught by the ship in the most efficient way. The vessel is equipped with two headers from Vélfag and two filleting machines, one from Vélfag and the other from Breivik AS. A water-cutting machine from Marel removes all the bones from the fillets and can cut the fillets into portions, loins, and tails, depending on the market's requirements. Additionally, there are product sorters from Marel and Slippurinn, and a mincing machine from the German manufacturer Sepamatic.
The vessel is outfitted with advanced processing equipment provided
by trusted industry partners, including Optimar.
The main focus on board will be on processing whitefish fillets, such as cod, haddock, and saithe, as well as shrimp, which complements DFFU's production lineup. The shrimp line has a sorter from Style and two boiling pots from Carsoe. An IQF (Individual Quick Freezing) freezer will be used to freeze the shrimp, preparing it as a ready-to-eat product.
Boneless mince is made from the heads and guts and used for feed production. Boneless mince is also produced from backbones and cutoffs, which are frozen and used for human consumption. Onboard are ensilage tanks to ensure the full utilisation of the biomass from each catch. No waste from production will be discharged into the sea, except for bones. Skin will be frozen and utilised, for example, in producing collagen for food supplements and cosmetics.
Production onboard features a high degree of automation, with products moving automatically to and from the freezers to the ship's freezer holds without human intervention, partly due to the aid of a robot. Significant emphasis has been placed on crew conditions and facilities to minimise simple and physically demanding tasks and prevent accidents. Crew accommodations are spacious, and the onboard acoustics and lighting were designed with the crew's well-being in mind.
The crew's accommodation is bright and spacious. Photo: Kristin Stoylen.
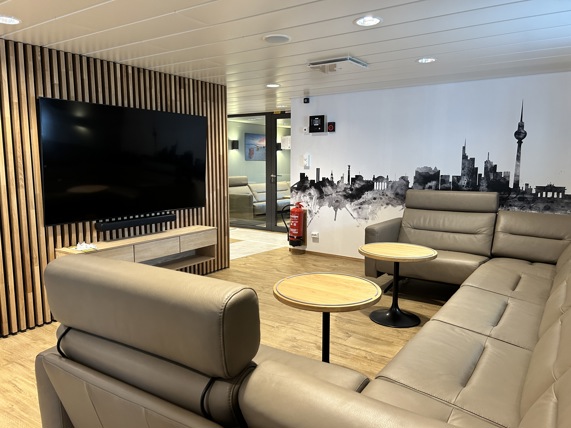
Baldvin Thorsteinsson and Samuel Rodriguez, Managing Directors of DFFU:
"The delivery of Berlin NC 107 is pivotal for DFFU, and VARD has done an excellent job. Over the years, VARD has built several technologically advanced vessels, consistently meeting the highest standard with their craftsmanship and innovation. Berlin NC 107 is equipped with advanced technical solutions from trusted partners. One significant change with this new vessel is its shrimp-catching and processing capabilities, enlarging the portfolio of products produced onboard. The production of whitefish has also been upgraded with new equipment, which increases options in production and expands our product range. The technology and equipment onboard will enable us to bring 100% of the catch to shore. This supports our goal of increased value creation at sea and directly aligns with our sustainability efforts.”
Gunnar Eik from VARD and DFFU's Baldvin Thorsteinsson after the vessel
was formally registered, and the German flag was raised.
Sigurdur Óli Kristjánsson and Teitur Björgvinsson, captains of Berlin NC 107:
"The enhanced production capabilities are exciting, and the new engines increase operational flexibility. From the crew's viewpoint, the upgraded working environment is a major improvement, with increased automation reducing the need for manual tasks. Another big change for the crew is better accommodation. The crew quarters have been designed to maximise daylight exposure, and special attention has been paid to ensuring healthy acoustics in the onboard factory. The main goal here is to increase comfort for our crew members. As captains, we are fully aware of the importance of this during long voyages at sea."
DFFU, located in Cuxhaven, is a subsidiary of Alda Seafood. DFFU is one of Germany's oldest remaining long-distance fishing companies, with a history spanning over a century.
Explore additional images of the new vessel captured in Brattvåg yesterday in the gallery below. Members of the media are authorised to download and utilise these images for their coverage but are asked to cite the photographer's name, which is included in the filename.